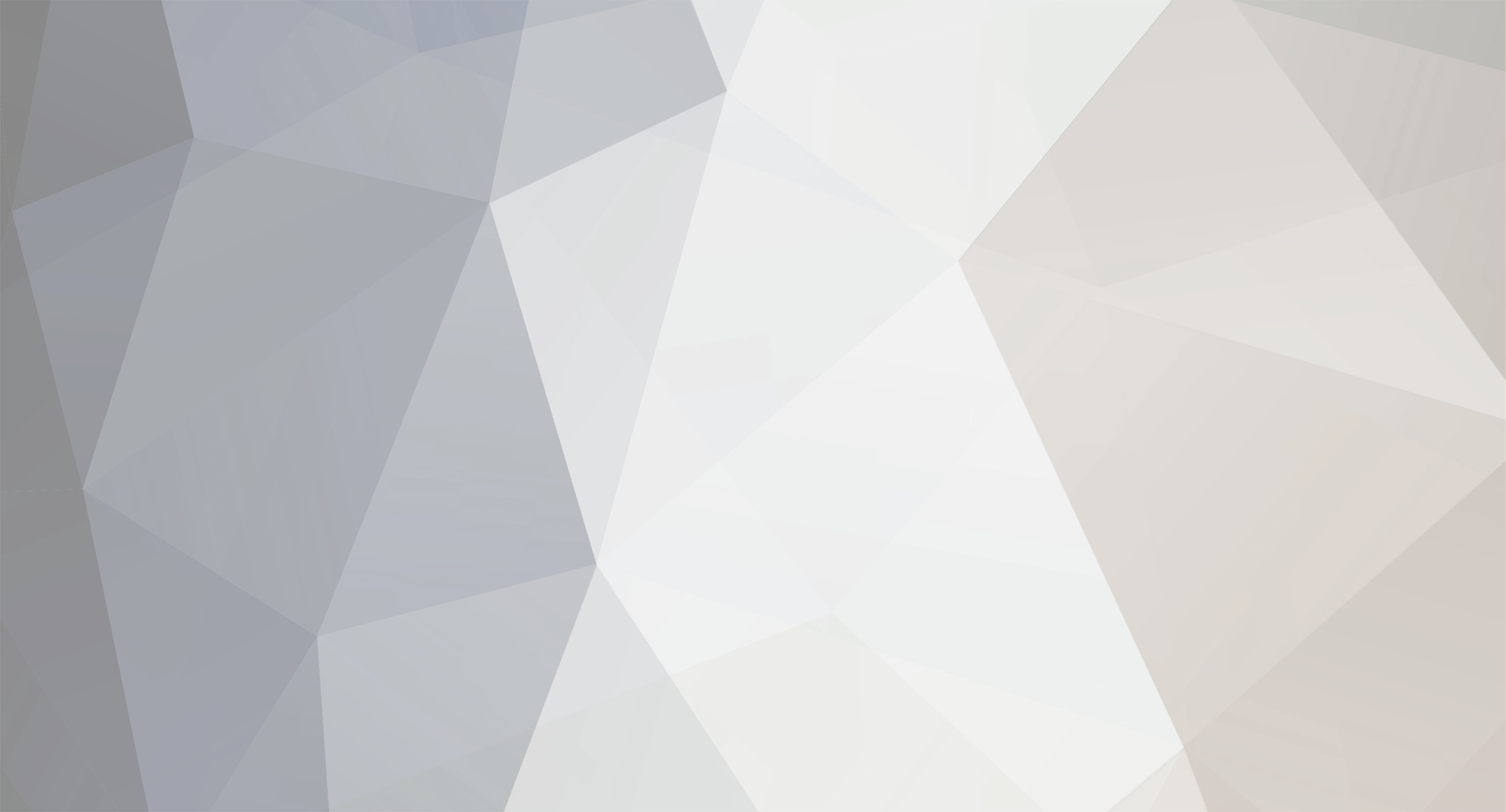
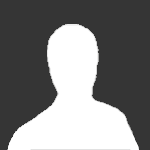
chaff.g
Members-
Posts
127 -
Joined
-
Last visited
Content Type
Profiles
Forums
Events
Gallery
Everything posted by chaff.g
-
It's actually not the lacquer surface that affects this decision, it's the enamel. What you want to avoid is interaction with the enamel thinner since you will be cleaning the enamel off the surface after applying the wash. So you can use either a lacquer or an acrylic coat. I think most people airbrush Future (an acrylic sealant) for this task, but it sounds like you're working with rattle cans. A popular acrylic gloss coat people like to use with Gundam models is called Topcoat, but this can be expensive and hard to come by these days. Alternatively, you could go to your local hardware store and easily find a clear gloss lacquer in a spray can. This will be the least expensive option.
-
You should never attempt to do a panel wash without first applying a gloss coat. The paint will just soak up the wash and leave the surface stained. Also, the capillary action which pulls the wash through the recesses won't work as well. I haven't found Gundam markers to be that useful to be honest -- there's no magic to them, they are just regular markers with a Gundam logo on them. Going over all those lines will take a long time with a marker and won't look as good as using something like Tamiya Panel Line Accent Color. I think simply doing a panel wash with an enamel will be easier -- it's basically idiot proof as long as you apply it to a gloss coat. It will also yield a much nicer result than would markers. I don't think I would try to apply decals to a semi-gloss surface if I could help it. The decals won't want to stick to the surface, especially if you don't have any setting solution. You'll achieve the best results if you apply the wash & decals to a glossy surface.
-
I think you're asking what kind of paint he used for the panel wash. It looks like he used thinned gray enamel paint to me. You can either buy some enamel paint and thin it yourself with enamel thinner, or you can buy something pre-mixed such as Tamiya Panel Line Accent Color.
-
Thanks for doing the experiment and reporting the results! I had to discover by trial and error exactly what solvents could safely strip lacquers without interacting with the styrene. Alcohol doesn't work at all; oven cleaner and automotive degreaser work OK, but usually require some work with a toothbrush to remove every last trace of paint from recesses. Of course enamel thinner simply destroys the plastic. Turns out the simplest solution is what works best -- just use Mr Color Thinner. I believe this solvent is very safe, as I have left styrene parts submerged in Mr Color Thinner for days at a time and they always emerge unscathed. It makes sense, as it would be bad for business if Mr Color Thinner melted Gundam models :-) Once I discovered it was not only possible, but very easy to strip lacquers, I became a lot less timid about applying paints because I knew there was a simple way to get a do-over. If you have some available, you might also repeat the experiment with Tamiya thinners, as they are more easily available in North America. In hindsight, I suppose the material the bottle is made of is a big clue. The hardware store stuff tends to come in a metal container while the Mr Color Thinner comes in a plastic bottle.
-
This time I'll apply a wash to the panel lines and fix the circular mask on the backpack. In preparation for a panel line wash, I airbrushed unthinned Future over all the white surfaces. A few parts after applying Tamiya Panel Line Accent Color Gray to the panel lines. The smooth surface coated with Future allows the enamel to flow smoothly through the recesses. The enamel collects in pools at the point of contact between the brush and surface. These are removed in the next step. The same parts after being cleaned with a cotton swab dampened with Zippo lighter fluid. The dark grey enamel remains in the deepest recesses, but the white surface of the parts are bright and clean. A closeup of the legs after applying the enamel wash, and a shot of the legs after they have been cleaned. Stripping the paint off the poorly masked backpack dome was easy. I filled a Ziplock bag with a small amount of Mr Color Thinner along with the backpack part. After sealing the bag, I filled this ultrasonic cleaner's reservoir with water and placed the bag inside. Mr Color Thinner easily dissolves cured lacquers, enamels, and acrylics but will not harm model kit parts made from polystyrene plastic. It does such a good job that utilizing an ultrasonic cleaner is probably not even necessary, but I wanted to demonstrate the technique. After a few minutes in the cleaner, the part looks brand new. To create a custom mask for the circular portion of the backpack, I'll cut one from masking tape. This is Tamiya masking tape stuck to a styrene sheet. I measured the diameter of the dome and used this X-Acto compass to cut a circle in the tape of the appropriate size. I wouldn't actually recommend using this particular compass because I found that the markings on the ruler did not accurately measure the circle that was scribed. The compass cut a perfect mask. I covered the rest of the part to ensure a clean result. Much better!
-
I think you are right about the canonicity of the seam. Unfortunately, the two halves of the main body are hollow and didn't come together on my build to create a line of uniform width. The gap just didn't look very good. I think a result that would both look good and also retain fidelity to the source material would probably be to fill the seam and then rescribe a line.
-
Thanks for the comments everyone! This time I finally get some paint on the main aircraft. Before continuing with the rest of the aircraft, I filled the gap between the upper and lower portions of the main fuselage with Mori Mori polyester putty and sanded it smooth. To break up the white surface of the aircraft, I decided to go with a two-tone look. After priming all the surfaces with Tamiya Surface Primer (Gray), I masked off some of the areas that I wanted to appear slightly darker on the finished model. On top of this mask, I sprayed a coat of Tamiya Fine Surface Primer (White). The contrast between the two primers is stark now, but will become very subtle after layering over base coats of color. Next, I airbrushed Mr Color GX 2 black across all the panel lines of the model. The shading will subtly emphasize the separation of the panels in the final finish. Closeups of the preshading follows. I started airbrushing Mr Color GX 1 Cool White onto all surfaces. The part on the bottom of these images has been painted white and the preshading is barely noticeable. In person, the shading is more pronounced, but it is still very subtle. A closeup of one of the intakes. The two-tone effect achieved by varying the shade of primer is clear in these photos. The wings after painting. Because there is no convenient way to attach an alligator clip to these parts, I taped them to a patch of cardboard to hold while airbrushing. The color separation is visible in these photos. The preshading came out quite nicely on the vertical stabilizers, but it will be covered by additional details later. The white base coat is finished. I like the two-tone effect the two primers created, but it was tedious to match the shades of grey on the various parts. In the future, I think I will use a uniform coat of primer and simply mix the whites I want. Next comes the red details. I masked off the red portions of the vertical stabilizers and the dome on the backpack and airbrushed Mr Color GX 3 Hermann Red. This is a pretty decent match for the reds found in the decals. To mask off the round dome on the backpack, I approximated a circle by forming a many-sided polygon surrounding the dome with many lengths of masking tape. Unfortunately, the polygon poorly approximated the circle. I'll strip the paint on this part and figure out a different way to mask this part later. The tips of the vertical stabilizers came out nicely. Next, I prepared a mask for the various black markings found across the surface of the aircraft. Hasegawa provides decals for many of these, but for such simple curves, it's must less hassle to simply mask and paint. It also yields a much better looking result than would decals. The blacks came out great as well. This thing is starting to look familiar :-)
-
Probably just CA glue. Unfortunately, I received the magnets after I had finished work on the strike parts so it was too late to incorporate them into the build. If I had it to do over again, I'd definitely magnetize the packs for that little extra bit of flexibility. Though, I'm not too bummed about it because the aircraft looks odd without the strike parts attached -- the legs are not poseable and neither is the tail which is in a fixed folded down pose.
-
1/48+fp's, 1/60+fp's, 1/72, 1/2k, 1/3k,1/100 and now 1/144
chaff.g replied to VF-18S Hornet's topic in Toys
These shots are just incredible. I, and I'm sure many others on this board, would be very grateful if you could find a little time some day to describe the technique, gear, and setup you use to capture shots like these. -
Agreed. I have no skill with Illustrator, but was thinking about scanning the decal sheet and sending it to Samuel Decal to have some produced. haven't gotten around to it, though.
-
Very nice. Your rescribed doors look much better than mine turned out in the VF-1 strike thread. What kind of putty did you use?
-
An update some assorted metallic parts. Before painting the body of the aircraft, I wanted to finish some of the small metallic bits such the vents, intakes, and exposed machinery. First, I primed the parts with Alclad 2 glossy black primer. Since this is an enamel, I left it to cure overnight before continuing. I gave the insides of the vernier thrusters a coat of Alclad 2 copper. I hand brushed the two pipes which extend to two of the smaller thrusters with assorted Citadel acrylic paints. Afterwards, the pipes were given a heavy wash of Tamiya Panel Line Accent Color black. Before airbrushing the exterior of the vernier bells, I masked their copper interiors with balls of sticky tack. I gave the exposed machinery on the main body of the aircraft a coat of Alclad 2 steel and magnesium. I airbrushed the exterior of the vernier bells with Alclad 2 steel. To make the exteriors of the thruster bells shine, I airbrushed a coat of Mr Color GX 100 Super Clear III. A shot of the finished thruster bells. I attached the small bells to the FAST Packs with CA glue. I think the copper of the bells creates a nice contrast with the dark teal of the packs.
-
I think this is the sequence you mean: Looking at the model, it seems like it could be done if the neck was extended somehow. Maybe if a riser was inserted between the hull and the base of the neck.
-
This time I'll show how I attached the head covers to the underside of the fuselage. Each head has a corresponding cover which it tucks into in fighter mode. Since the heads are removable, the covers need to be as well. I decided to magnetize them just like the heads. I fashioned two pylons out of a short length of styrene rod and CA glued a magnet to one end. I placed them such that they would be hidden when the covers are attached. The pylon was cut such that the end of the magnet is just flush with the aircraft. Both pylons in place. I put mating pylons on either side of the head covers. Since the pylons on the covers were so short, I reinforced them with a little bit of Mori Mori polystyrene putty. The cover fits perfectly. You can see how much of the head will be hidden by the cover when the aircraft is complete.
-
Cockpit is already looking fantastic!
-
If you have a grey primer, I would prefer that to black. A black primer will be difficult to cover, especially with the tan & grey paints because lighter paints are translucent. If you haven't bought paint yet, I would just pick up the grey Mr Surfacer. It will take more coats of paint to get good coverage over a black primer, and each successive coat of paint will introduce opportunities for problems: dust settling on the paint, thick paint obscuring detail, fingerprints, etc. The modeler from the diary you found probably used the black primer to paint the base of the model, or maybe some of the metallic details. I would probably use a mask and the spray can for these areas. Masks don't always work that well with brushed-on paint. Besides, if you're using a brush, you could just control where the paint goes. You might also consider inverting the mask you proposed - paint the parts tan first, apply the mask to the tan areas, and then spray with grey. It just depends on how adept & patient you are at applying the mask. If it was me, I'd start by spraying these areas. If necessary, you could go back and touch up the nooks and crannies which the spray missed with hand-brushed enamel paint and a small brush.
-
The A head can be assembled without the sensor housing and a different sensor can be used instead: I assume this is the SDFM A sensor.
-
It looks like he sprayed the blue parts with Mr Finishing Surfacer 1500 Black. This is just Gunze's brand of black surfacer/primer. The blue he's going to use is the can labeled 14 - Mr Color Spray Navy Blue. I'm almost certain that all of these are lacquer-based paints -- not acrylic. (Tamiya and Mr Color spray cans are lacquer paints) I've never actually encountered an acrylic paint in a rattle can. If you are in the United States, it would be easier to get ahold of the Tamiya spray paints rather than the Mr Color Sprays. The paint sequence I would use would be: 1. Primer 2. Color coat 3. Gloss coat 4. Decals 5. Semi-gloss or matte coat You could optionally add another protective gloss coat after the decals before step 5. If this is your first kit, I actually think doing the detail with Gundam marker or similar and masking off and spray painting the grey parts of the legs would look fine. A final semi-gloss or matte clear coat will blend the surface texture together. There would be a bit of a color mismatch between the grey-molded cannons and grey-painted hull, but that's a feature, not a bug :-)
-
All done! Here are some glamour shots. Remember, almost all of this detail will be completely invisible when the heads are attached to the aircraft!
-
Next I detailed up the A head's visor. You can see that the transparent piece has molded detail. The idea will be to enhance this detail. To bring out the detail on the A visor, I used black Tamiya Panel Line Accent Color. It collected into the corners of the raised detail. With the details enhanced, they're more visible when viewed from the exterior side. I cleaned up the details with Zippo lighter fluid and masked the exterior surface. To make the details as visible as possible, I airbrushed the interior surface with Alclad 2 chrome and followed the chrome with a layer of Alclad glossy black primer. The glossy black will ensure the chrome layer is as shiny as possible. Because the glossy black paint is an enamel, I set the part aside for a couple of days to cure. I preshaded both heads with acrylic Tamiya smoke and followed that with a layer of Mr Color GX 1 cool white. For the recessed black details on the A head, I carefully masked them off and airbrushed Mr Color GX 2 black. The details are nice and sharp after removing the mask. I also added the housing for the A head's visor, finished in Mr Color GX 2 black. Since most of the S head's lasers are a metallic color, I masked off the white parts with sticky tack and sprayed a coat of Alclad 2 black primer. After curing, I followed this up with Alclad 2 steel. Test fitting the A head. I detailed panel lines with Tamiya Panel Line Accent Color - gray on white parts, black on metallic. The kit comes with extensive decals, but does not include enough decals for both heads. Instead, I masked off an area for the red arrow marking on the A head and airbrushed Mr Color GX 3. I think the result is pretty convincing. Like many Studio Nue designs, the S head's visor is always depicted in line art surrounded with a thick black band. I masked off this area and hand brushed Citadel chaos black. After removing the mask, you can see this was a mistake -- I should have airbrushed it on. I tried to clean up the black as best I could. By this time, the enamel on the A head's visor had cured, so I removed the mask. The details stand out perfectly. After a coat of Mr Color 138 clear green, the A visor is finished.
-
Mori Mori comes in two parts -- the greyish purple filler material and orange hardener. To use Mori Mori, you mix the two parts together. The material looks and feels like yellow mustard and smells comically bad. To fill the neck, I just sort of gooped it in and scraped excess off with the included spatula. I waited a few hours for the putty to cure and then sanded it smooth. For good measure, I filled the post on the fuselage with the leftovers. To add the posts back, I drilled a hole and cut a couple lengths of styrene rod of the appropriate diameter. To find the right spot to drill into the base of the S head's neck, I painted a small dot into the center of the magnet on the fuselage. I slotted the S head into place on the fuselage, and the paint left a mark where I need to introduce the hole for the sister magnet. I was impressed with the Mori Mori's ability to retain very fine detail. This is a 1.5mm or so circle, and the edge of the hole is sharp. Another kind of putty would have just crumbled. The magnet fits perfectly inside and the S head is perfectly oriented facing forward thanks to the guide posts. Next I painted the A head's laser. I need to finish this before the rest of the head because the A head parts wrap around the laser. I began by preshading with acrylic Tamiya clear smoke. After preshading, I airbrushed a layer of Mr Color GX 1 cool white. I hand brushed the joint with Citadel boltgun metal. I airbrushed the middle part of the A head with Mr Color 13 neutral gray and then masked it up. I inserted the laser and used plastic cement to fuse the halves.
-
Next, I airbrushed the visor transparent green with Mr Color 138 clear green. I finished the visor by submerging it in Future to make it as shiny as possible. While the coat of Future was curing, I painted the interior of the S head Mr Color 13 neutral gray. The purpose of this step is simply to ensure that if any of the interior of the head is visible through the visor, it is a neutral color. I attached the detail and visor using CA glue. The effect is pretty decent. Various features of the metallic detail are visible through the transparent visor. Testing the finished visor inside the S head. The detail adds quite a bit upon scrutiny. To continue with the S head, I'll need to surface it. That means removing the seam line that runs down the axis of the face. I masked up the visor to protect all the hard work so far. Masking tiny, curved parts like this requires lots of individual pieces of tape. I used plastic cement to fuse together the halves of the head and also coated the exterior of the seam. For good measure, I also added a layer of Mr Surfacer 500 to ensure any depressions were filled. While the S head cured, I started thinking about how to magnetize the aircraft hull where the head will attach. There's not a lot of material to work with. I marked the midpoint between the two holes which are intended to receive the posts built into the base of the neck. I realized that without these posts (I cut them off of the S head), the heads would not be correctly oriented looking forward. On the flip side of the fuselage is a post which fits into the fuselage's upper half. I was worried that drilling a hole into this surface large enough for the magnet I showed earlier (3mm) would damage this post. So I changed my mind and went with a smaller (1.5mm) magnet. Test-fitting the A head. Because it retains the two posts, it is perfectly oriented. I drilled a hole into the base of the post and fit the smaller magnet in. The smaller hole goes right through the middle of the post. Filling the post with CA glue both fused the magnet to the surface and reinforced the post. Since I decided to go with a smaller magnet, I need to redo the hole in the base of the neck of the S head. That means filling the neck with a material that can be drilled into. For this purpose, I used Mori Mori, which is a two-part polyester putty often used by Japanese figure sculpters. On the left, the S head's neck needs to be filled with putty so it can be re-drilled to receive a magnet hole sized like the A head on the right. I'll also reintroduce the two posts to ensure the S head has a proper orientation.
-
Next I'll finish the heads. This kit includes options for both the S and A head variants of the VF-1. I'll include a modification that allows swapping the heads on the finished kit. Most of the work I did here is entirely superfluous -- the finished kit obscures almost all the detail beneath the brow of either head. You can see that the interior of the S head is visibly empty behind the visor. Later I'll fill the void with some scratch-built detail. To enable parts swapping the heads, I'll magnetize them with neodymium magnets. I began by drilling a hole for the magnet into the base of the neck and progressively used larger bits to widen the hole. Eventually I had to hand turn the bits as they became too large for the drill. You can see that the circumference of the hole became untidy. The magnet is around 3mm wide. I chose some option parts usually used for the monoeyes of Zeon Gundam kits to use as the S head's camera. The green jewel fits into the metal housing. It's just the right size for the S head's camera. The S head in profile. You can see that there's plenty of room for detail behind the visor To add a bit more detail to the brow of the S, I drilled a hole into the circular depression. I'll fill this later with a tiny length of fiber optic. I built up a base for the camera using some plaplate (plastic styrene sheets). On the right, the camera mounted on the housing. It will fit snugly between the visor and back plate. I finished detailing the base with some round option parts and tiny pieces cut from round and square plastic rod. Test-fitting the detail inside the head. To maximize the visibility of the detail behind the visor, I'll paint it chrome. The idea is to maximize the amount of light reflected. I airbrushed a base layer of Alclad's glossy black primer. Over the top of the glossy black base, I used Alclad 2 chrome. You can see that the result looks very metallic.
-
This time: missiles. After the hardpoints and pylons were magnetized, next I finished the missiles. These are the large reaction warheads pictured here, and micro missiles that fit into the missile pods and FAST pack booster. After assembling and fixing surface details, I airbrushed a coat of Mr White Base 1000 thinned with Mr Leveling Thinner. Mr White Base 1000 is essentially white Mr Surfacer 1000 - a lacquer-based primer. I airbrushed the tips of the RMS-1 warheads with Mr Color GX 4. I pre-shaded the RMS-1 missiles with Tamiya X-19 smoke. This is a transparent grey. It comes out a little brown, but the base coat of white will cool it down. I airbrushed the missiles with a coat of Mr Color GX 1. The preshading is barely visible but applying a wash to the panel lines will emphasize the gradation. I used Tamiya Panel Line Accent Color grey to bring out the panel lines on the white surfaces, and black on the yellow. After applying decals, I gave the missiles a protective glossy coat of Mr Color GX 100 Super Clear III. I only finished the tips of the micro missiles because the rears won't be visible when housed in the missile pods. Closeups of the panel lining. The lines on the RMS-1 missile are a bit broken because the lines are not sunken channels -- these details are ridged rings that wrap around the missile. You can see that the decal itself wraps around the ridge. After panel lining, I applied another coat of Mr Color GX 100 Super Clear III to protect the details. Finally, because I wanted a semi-gloss look on the white surfaces of the aircraft, I finished the surface by airbrushing a coat of Mr Color 181 Semi-Gloss Super Clear. The contrast between the matte FAST packs and glossy white aircraft should be interesting. The finished RMS-1 warheads attached to pylons and micro missiles in their housing. The finished UUM-7 missile pods. I think it's cool how the metallic pylon magnets add detail of their own. The finished RMS-1 reaction warheads. Next time: magnets and monoeyes.
-
Thanks guys! I hope if someone sees this and tries it on their own they learn from my mistakes :-)