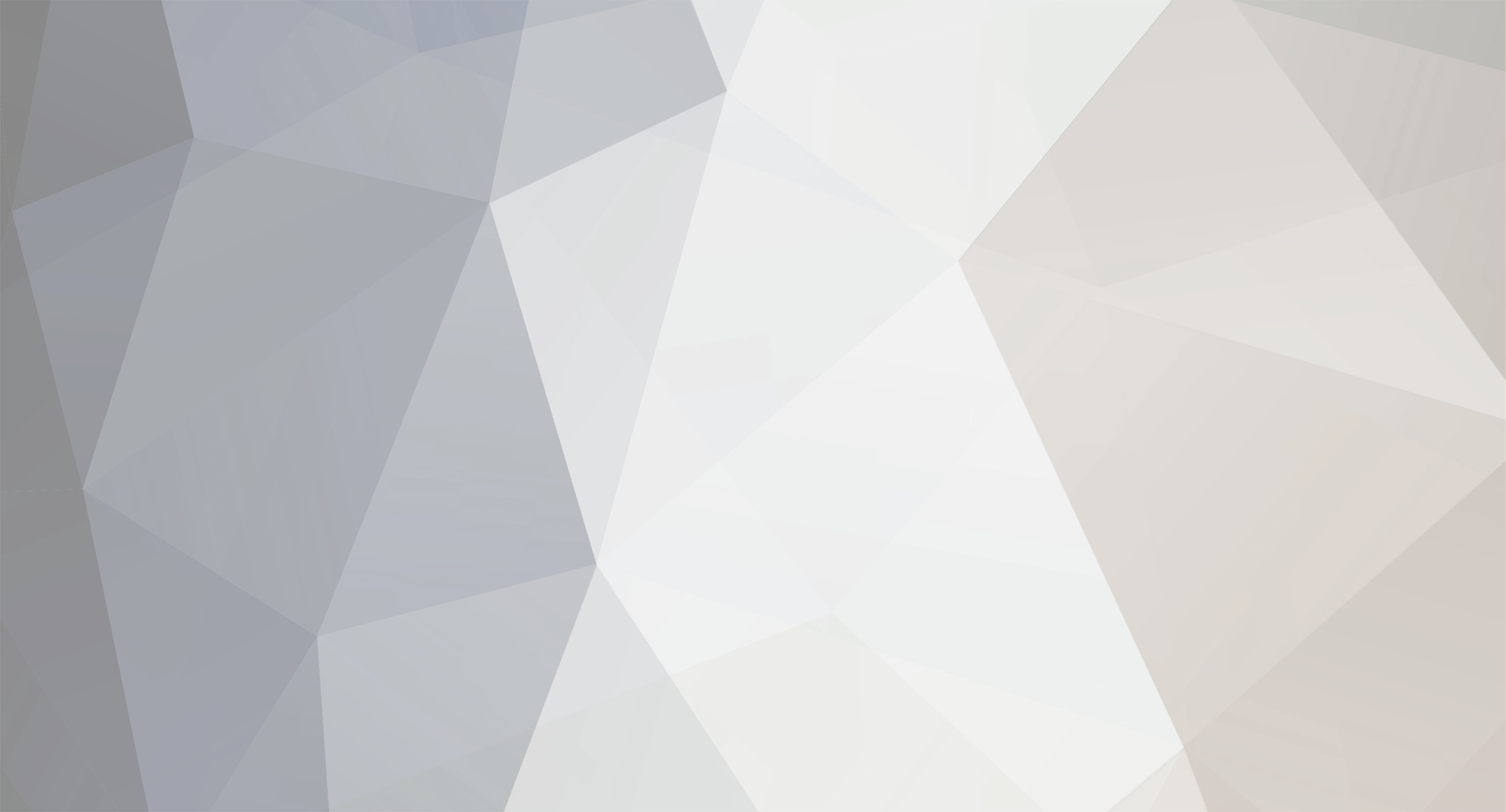
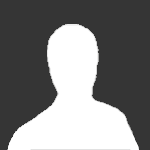
mslz22
Members-
Posts
1144 -
Joined
-
Last visited
Content Type
Profiles
Forums
Events
Gallery
Everything posted by mslz22
-
Just out of curiosity... That "bad" resin wasn't Smooth On, was it? 383219[/snapback] Yep, Smooth-On, depending on the part i use either Vagabond or Smooth-on 321, both cure to about the same color but the 321 is a 7 minute resin and the Vagabond is a 3. For some reason the 321 will leach if the B part is "off". I have used it for at least the past 2 years without a problem (although it takes much more stirring to avoid problems) , but i just am suprised they sent me resin from the same batch 2x. I was really upset yesterday, but they are replacing it at no cost and picking up the bad batch....just more delays.
-
Even i can't believe it but they sent me replacement resin for the bad resin.......ready for this.....from the SAME BATCH Seems like the shipping dept did not get the notice TO STOP SENDING THE BAD RESIN OUT.....AHRHHHHHHHHHHHHHH
-
My first pour out of the bad batch was not a mold for the monster, it was for another project. Luckily my eye caught the resin starting to leach in what was left in the mixing container and i pulled out the part before it got the mold messy.... mike
-
It will not cure right, and is leaches the part B....making it oily.....it happens from time to time, but my last bad batch was about a year and a half ago so i guess i was due.....
-
Ok, bad news.....well not that bad, but delay news....I am out of resin...not because i did not order it, but because the batch that i just got is a bad batch....10 gallons worth of spoiled resin...replacement resin is on the way, but may not be here until tuesday...so look for the first orders to be taken later next week...sorry i get a boatload of work done on the weekends and now i am stuck..... sorry guys mike
-
Gosh i love Monsters...all shapes, all sizes.....
-
I expect the molds to hold for at least 35-40 kits, keep in mind that for many parts i will be making multiple molds, so those will go even further. As for the master breaking, i take whats called a "protection master" using a special tooling resin, so if i need to i can make a new mold of any of the parts..... The only mold that i would be concerned with as far as diminishing quality would be the large body mold, however most problems with a mold arise from deep undercuts or a large about of prominent detail, while the monster body is detailed it does not have a lot of parts that would be prone to ripping out, that added to the fact that i use one of the best mold materials that i have found, should get us enough kits, if i need to i will simply make more molds
-
I have 10 sets on hand so it will be fine.... mike
-
just got a package from devin, just need to open it up and see how many sets are in there....
-
Quick update for everyone, i just poured the mold for the engine cover, that is the last of the big molds, i now need to concentrate for a couple of days on making multiple molds for the small parts and finishing the hinge pattern. Unless I hit a snag i will anticipate taking $ for the first 5 orders early next week and shipping those out within a week or so of payment, i will be starting a for sale thread over the weekend. Keep in mind that the instructions will likely be in process when the first are shipping.... mike
-
The balsa foam/balsa wood was covered with a skimcoat of lightweight bondo, i would have prefered to cover it with styrene but think that would not have worked on all of the curves that the body has. I ended up being happy with the balsa/bondo combo because I tweaked the body over the course of building and i am not sure if i would have been able to do that as easily with the styrene. If i was building something along the lines of say.....Oh 1/2500 DYRL SDF-1 that does not have so many curves i would likely use a harder wood and cover that with styrene....if i was going to build such a thing.....
-
Not sure at the moment, need to catch my breath for a moment, anyone just checking in see page 23 for mock up pics....
-
-
-
-
Wow, what a weekend......95% of the molds are done, some small detail parts need to be molded still and the engine hatch....i need some sleep anyway here are some pics of a mock up, the valk is a 1/60, not a 1/72, the valks in the back are 1/48's, it is a bit sloppy because it is not really glued together, just pinned together, hence the paintcan support........
-
I was wondering, how come the master pattern was destroyed in this process? 379558[/snapback] The basic frame of the body was made largely of balsa and balsa foam, it was really really fragile, but the body has some curves that needed to be carved and balsa and balsa foam are easy to carve....
-
I'm not too concerned with any kind of tipping over, the feet are solid and heavy themselves, and the body is still hollow, as are most of the arm cannons, the main cannons etc. The thing that will be very important for modelers is to get a good glue bond between the upper leg part and the detail part that gets glued to that, mostly they need to be glued before painting. Also the instructions will show you how to add a 3/32 brass pin to that part.... the seam lines will not cause any type of distortion of the body like what you are describing with the SMT (keeps fingers crossed) , i think the worse will be needing to rescribe a panel line or such...
-
-
some pics with the other 1/72
-
-
-
Ok, this morining i had a dentist appointment and then had to spend most of the rest of the day with my wife....ouch, i will let you guess which hurt more Anyway, i just cut the monster body out of the mold and ran thru the first casting...so here we go, the good the bad and the ugly....... The Good, very workable mold, first shot and i had no bubbles in the body, overall the first casting was good, some problems with the registration, but that was my fault for not using enough rubber bands and once resin starts to seap out of a mold, it is near impossible to get the registration back to 100% The Bad, well not really that bad but, the sockets for the main upper cannons will need to be drilled out instead of being molded in, the reason, being molded in locked the body into the mold so i had to cut the rubber in that section. that won't effect you guys, i will drill them in (as i did in the following pics), just more work for me .........Also, i needed to cut the mold in a way that i could get the body out, that ended up putting a seam line in some spots of the body that i would have liked not to have the seam line, but the mold good enough that the seam line is very easy to clean, i did this first casting clean up in about 15 minutes....also the casting is a bit heavier than i expected, when working with modeling board it is hard to determine how heavy the final casting will be, even hollow this one comes in close to 3lbs, not a big deal, still much much lighter than the other 1/72. The Ugly, this thing is huge, about $250.00 worth of rubber, and the pattern was destroyed so i will be taking a low shrink "protection copy" incase i ever need to remake the mold. without any further rambling.....pics for you....the panel lines are still not really showing up with the bright shop light but they are there....
-
Thanks for the offer, while i've never made a mold that big, that is pretty much the method that i used for the monster body. I've used that method countless times before and often prefer it to the traditonal 2 part mold, but it usually depends on the part i am molding. Again, thanks for the offer... mike
-
Well i just finished pouring the mold....i lost track of how much i used but i bet this mold is in the $200.00 range at this point...i will weigh it tomorrow. The bad part about making something hollow is that the hollow part inside ends up needing to be filled with mold material. In the long run i will get more castings since the resin castings will be a lot less resin and not get as hot, therefore not burning the mold out fast. I went thru a few versions in my head as to the way that i was going to make the mold. I actually started to clay the whole thing up as a traditional 2 part mold, but once i started to do that it just became unreasonable for a number of reasons, and would have cost me even more than the way that i ended up with. I ended up mounting the monster to a mold box and poured it as a 1 big pour (in many many stages) , i added all the proper venting, and will cut out the pattern from the mold tomorrow, using a mold key knife and following premarked lines.....and i fully expect the pattern to be nearly destroyed upon taking it out.......all and all this is the toughest mold out of all that i need to make, so keeping my fingers crossed...it can only get easier from here.... mike